NEWS ARTICLE
Efficiency, Energy & Emissions Whitepaper
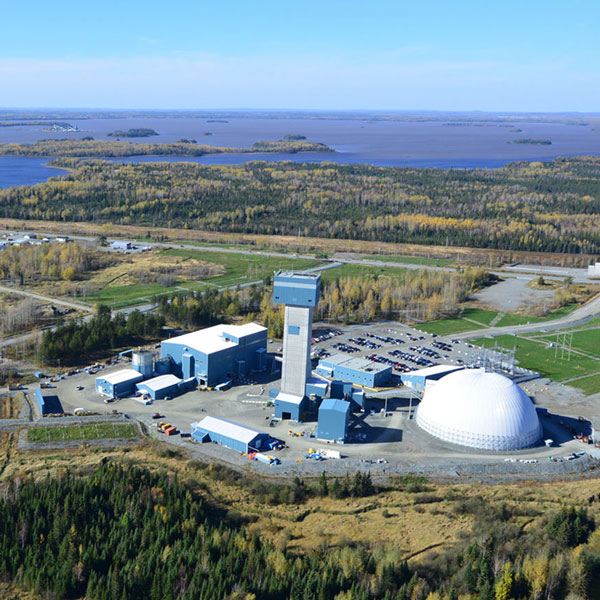
Executive Summary
This case study explores the transformation at Agnico Eagle Goldex Mining Complex through the implementation of the Railveyor system. The results showcase significant operational efficiencies, cost reductions, and environmental benefits, including a decrease in emissions. Agnico Eagle’s forward-looking approach positions it well to meet operational challenges and future emissions targets.
Agnico Eagle Mines (AEM) conducted an internal analysis comparing Goldex’s site-wide emissions using Railveyor as the primary haulage method versus a simulation of site-wide emissions using a fleet of diesel trucks as the primary haulage method.
Their conclusions clearly show (Figure 1) a significant emissions reduction through the utilisation of Railveyor – up to 39% when compared with truck haulage. It should be noted
that there is a significant “baseline” of emissions that are not affected by material haulage fuel
source type.
In AEM’s efforts to decarbonize operations, Goldex is a stellar example of a mine leading the way towards Net Zero.
Challenges of Mining Deeper Zones
Located at the western exit of the city of Val-d’Or, Quebec, Goldex is an underground gold mine that restarted commercial production in 2013 using the method of long-hole stopover with paste backfill to extract deposits. The mine faced some challenges with developing deeper zones in a low grade ore Mine.
Economics
- Low grade ore: Low grade ore required a highly efficient and cost-effective haulage
system to keep OPEX down. - Deeper zone, longer haul: The deeper and longer haul routes also posed significant
logistical challenges to truck haulage. Transporting ore over longer distances increased
fuel consumption and maintenance costs, increasing OPEX. - Increased ventilation demand: Extensive ventilation was required to keep exhaust
and heat from diesel-powered haulage equipment within Occupational Exposure Limits
(OELs), further straining the mine’s cost structure.
Geotechnical Conditions
Geotechnical conditions suggested a material haulage technology that could follow a
flexible route design, putting traditional conveyors at a disadvantage.
Safety
With the need for a flexible haul technology, a fleet of diesel trucks was the obvious alternative to Railveyor. However, with increasingly long, complex haul routes come increased safety risks to drivers and other workers in the mine. An autonomous haulage solution that removes workers completely from material transport areas was desired.
These multifaceted challenges mandated an innovative approach to maintain profitability and ensure the safety and health of workers. Agnico Eagle needed a solution that could address the economic, geotechnical, health, and safety issues comprehensively.
Sustainability
Among Canadian mining companies, Agnico Eagle Mines is a leader in innovation and sustainability. According to page 18 of AEM’s 2022 Climate Action Report:
In 2021, the Board of Directors approved Agnico Eagle’s commitment to achieve Net-
Zero by 2050 and formal support of TCFD. In 2022, we are proud to announce that a
Net-Zero interim target of a 30% reduction in absolute Scope 1 and Scope 2 emissions
by 2030 (based on 2021 levels) has also been approved.
With these ambitious goals in mind, AEM has driven the industry forward as the company seeks to identify and deploy technologies that increase energy efficiency and decrease emissions.
Solution: Railveyor
The Railveyor system emerged as the optimal solution for Deep Zone One, offering a flexible, cost effective, and safe alternative to traditional haulage methods. Feasibility studies highlighted Railveyor’s advantages, including lower ventilation costs and the ability to handle larger rocks without an underground crusher.
The Railveyor team worked with Agnico Eagle to design a system that is loaded with a vibratory feeder connected to rock breaking equipment. The system consists of a 3km shuttle with bypasses which allow trains to transit from the load point to the discharge point and back with minimal tramming interruption.
With 91 drive stations propelling the trains, the Goldex Railveyor system connects the 1250 level to the 730-meter level. At this level, the Railveyor discharge loop safely unloads ore which is then hoisted to the surface for processing.
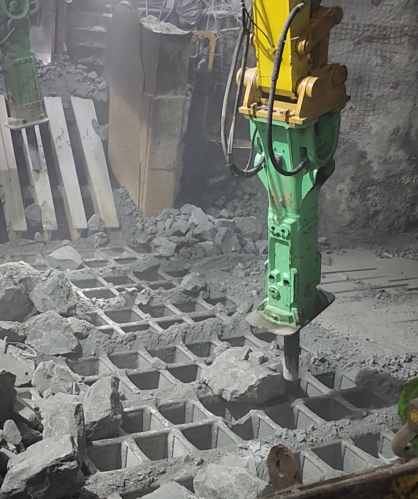
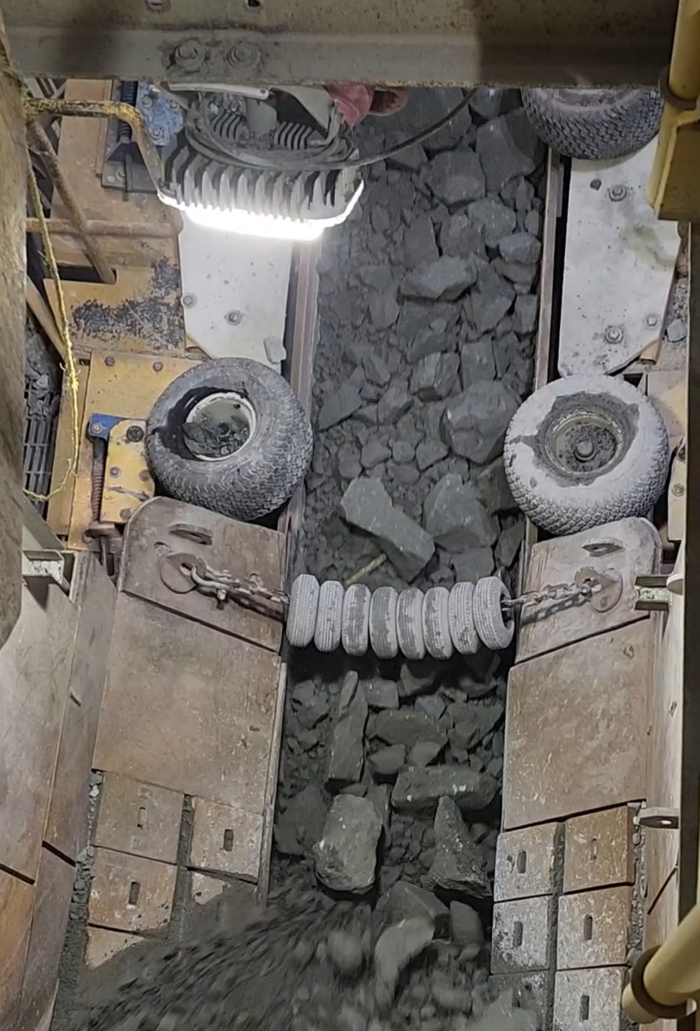
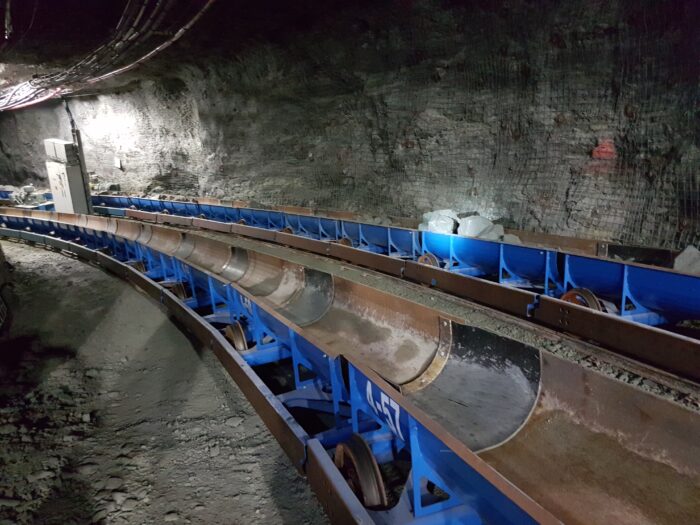
Production Targets Met & Exceeded
According to Agnico Eagle’s website:
“The Rail-Veyor system reached a milestone in the fourth quarter of 2020 with 5.0 million tonnes hauled since its commissioning. In late 2021, the system was operating above its 7,000 tpd capacity.”
“Goldex Railveyor has been optimized since 2017 resulting in strong production in the latest years. It integrates the latest technologies like LTE network and AI. It has proven to be in line with the energy consumption theoretical model. Energy comes from a reliable electrical grid, so costs are predictable and stable compared to fossil energy. Goldex Railveyor also shown upside on
productivity, industrial hygiene and health and safety.” Christian Lessard Maintenance Superintendent, Goldex
Energy Efficiency Estimates Validated
The energy efficient, all-electric system significantly reduced emissions at the mine. In a recent study from NRCan-CanmetMINING, the Goldex Railveyor system’s energy usage was measured and studied. The study validated the energy efficiency claims of Railveyor, with the system observed operating within 6% of expected energy usage levels calculated by Railveyor during system design.
Based on CanmetMINING’s calculations, the Goldex Railveyor system requires 0.989 kilowatt-hours to move one tonne of ore one kilometer. Factoring in Quebec’s average electricity price at the time of this
publication, the estimated cost is less than $0.07/tonne-km. According to Christian Lessard, Maintenance Superintendent at Goldex, that reduces OPEX by as much as 75% when compared with truck haulage.
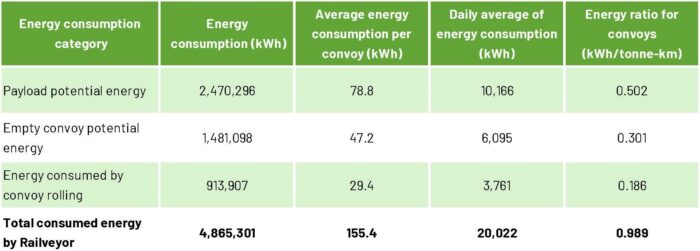
Figure 2: CanmetMINING table of Railveyor measured electricity consumption at Goldex over the
study period of 243 days
For further reading, please see “The Future of Energy-Efficient Haulage” in Global Mining Review.
Emissions Significantly Reduced
Agnico Eagle’s internal analysis showed that Railveyor is responsible for significant reductions in emissions. By comparing known emissions from Railveyor and emissions from a truck haulage simulation, AEM found that Railveyor reduces emissions from haulage as much as 39% over multiple years. We can extrapolate beyond the timeframe of the analysis performed by AEM. Logically, as the mine goes deeper in subsequent years, hypothetical trucking emissions – and costs – may increase further.
Other GHG-emitting activities also contribute to the overall totals reflected in Figure 3 – i.e, processing, small mobile equipment, and blasting. Sustainability consultancy Warm Springs Consulting (WSC) compared emissions and economics over several haulage methods. Isolated from emissions from other mining activities, WSC shows the dramatic difference (Fig. 4) between Railveyor’s emissions and other haulage methods.
Notably, the Railveyor at Goldex does not utilise regenerative drive stations to generate electricity on the downhill section while braking. Application of this technology could reduce overall emissions even further.
Figure 3: Site-wide Emissions Comparison at Goldex
Figure 4: Emissions and Energy OPEX between Alternative Haulage Methods