NEWS ARTICLE
Railveyor on Reducing Mining Costs
With consulting firm PWC highlighting cost inflation in mining as a growing risk in recent years, mines are focused on operational efficiency that directly improves project viability, life of mine, and the financial bottom line.
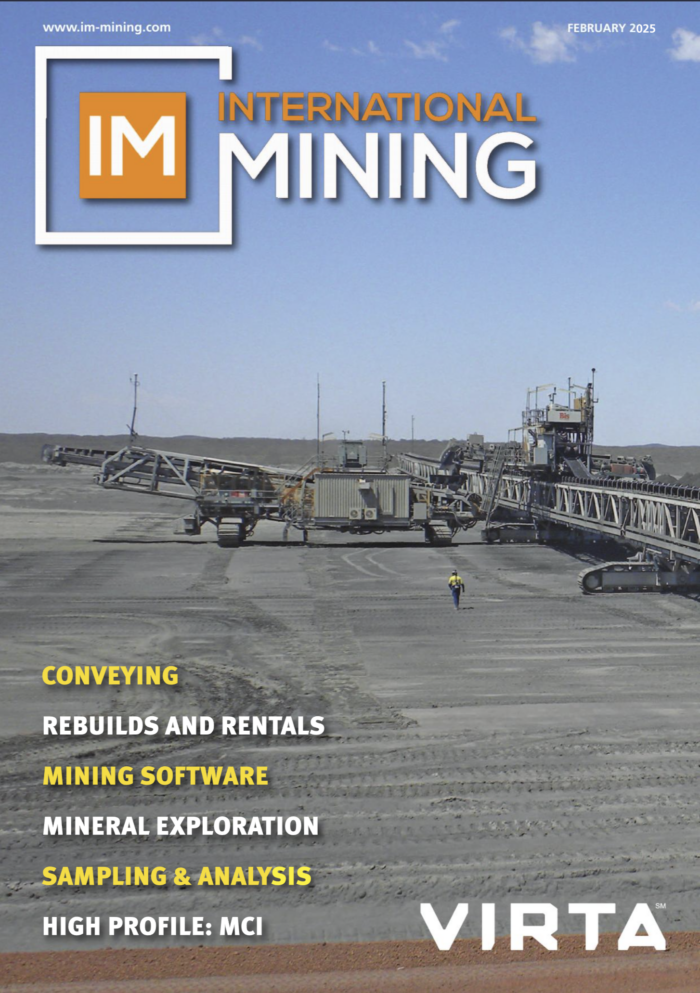
A productivity game-changer in materials handling has been Railveyor’s hybrid system that leverages the best aspects of rail and belt conveyor technology – while avoiding their limitations. These efficiency benefits also contribute to meeting strategic sustainability targets for lower carbon emissions.
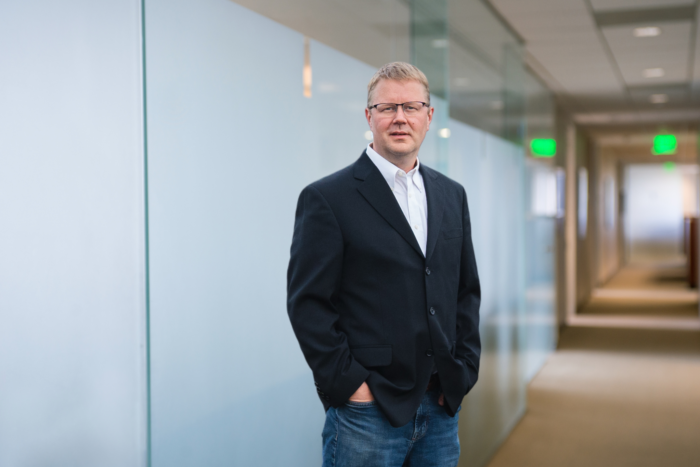
Russ Pietila, Vice-President of Product Development at Railveyor told International Mining: “While mining has long relied on rail, conveyors and trucks for materials handling – and developed a close familiarity with these technologies – financial and environmental pressures are leading to a growing appetite for transformative technologies like the Railveyor.”
Particularly where conditions demand the movement of material over steeper gradients and through tighter curves, the Railveyor provides much more flexibility than conventional rail or conveyor systems. While traditional conveyors are effective for long, straight and flat distances, they become costly and inefficient in complex terrain or extended runs with steep gradients.
Pietila: “Conventional belt conveyors are limited to gradients that avoid risk of material rollback. This often requires significant land grading or rerouting of conveyors, depending on the terrain. In contrast, Railveyor can manage gradients of 20-30%, facilitating more direct and cost-effective routing while limiting expensive infrastructure requirements.”
An important benefit of the tight turning radius is that it eliminates the need for transfer points. Apart from avoiding the considerable costs of chute infrastructure at transfer points, mines also reduce their risk of disrupting material flow when there are blockages, heavy wear or other issues at these points.
“Railveyor systems also demand less infrastructure to install, and are readily movable and adaptable. Unlike the graded roads and extensive ballast, sleeper and drainage elements demanded by traditional rail, for instance, Railveyor relies on light rail that can be installed on uneven terrain without the need for precisely graded surfaces. This means lower installation and maintenance costs as there are reduced earthworks, construction and road repairs necessary.”
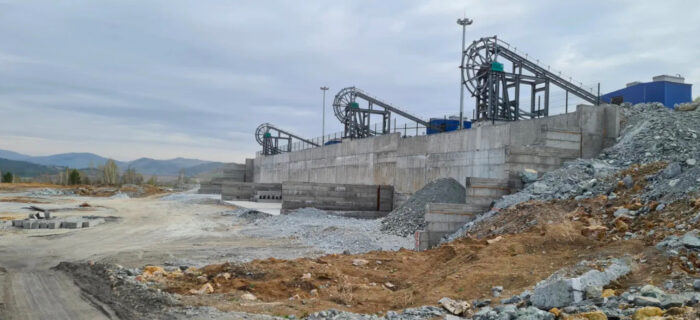
A perennial risk to mines is the unplanned downtime from a conveyor belt or component failure – potentially taking days to source and replace. By comparison, Railveyor’s modular design and fewer moving parts allow a train or car needing attention to be removed from the track for maintenance while the rest of the system continues to operate.
Leveraging the energy efficiency of steel wheels on steel tracks, Railveyor goes further by using electrically powered drive stations to ensure consistent energy distribution along the route. These motors power drive wheels or linear drive systems that propel the lightweight rail cars forward. During downhill or decelerating movements, the system employs regenerative braking to recover energy and feed it back into the power grid, enhancing energy efficiency.
Pietila says that independent analysis of Railveyor’s energy consumption shows that it achieves fuel-related emissions that are orders of magnitude lower in the long term than many traditional technologies. This has been observed and documented at an installation in Canada, which realised carbon emission reductions up to 39% when compared with the truck fleet previously utilised at the mine.
The system is fully autonomous, allowing for single operator control – regardless of scale. This contrasts significantly with truck fleets, which require more operators and supervisors as they expand. Railveyor also enhances site health and safety by reducing dust and noise levels, as well as the system operating on its own dedicated and predictable route path.
Applicable in both underground and surface environments, Pietila says that Railveyor has delivered proven value to mining customers in a range of applications for over 15 years. Among these is a South American customer in a surface application, who wanted a lower maintenance operation with less downtime compared to traditional conveyors, while also taking advantage of Railveyor’s flexibility that would allow for an overall reduced footprint for their haulage system.
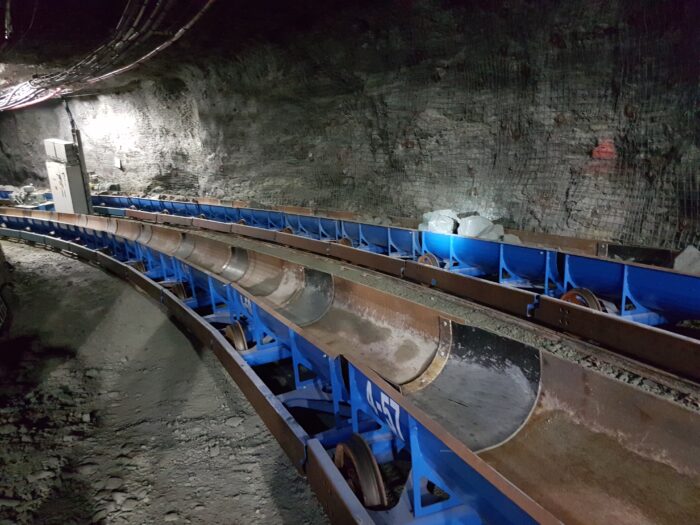
Similarly, at an underground operation at Agnico Eagle Mines’ Goldex complex in Quebec, Railveyor lowered operating expenditure by up to 75% and reduced carbon emissions by 39%. The flexibility of the Railveyor application allowed the mine to get closer to the ore body, increasing the life of mine.