NEWS ARTICLE
Voices of Railveyor: Michael Van Der Hooft
Throughout the years developing the Railveyor system, our team has made lasting connections within the mining industry and beyond. Professionals in engineering, operations, and leadership have contributed to the successes of Railveyor while objectively evaluating the promise of our technology. We believe there’s value in sharing the perspectives of those who have firsthand experience with our system.
That’s why we are launching Voices of Railveyor: a series of short, topical interviews available to view on railveyor.com and social media platforms like LinkedIn.
Few people are more respected by our team than Michael Van Der Hooft, a veteran mining industry leader who led the Vale Copper Cliff 114 pilot project – and the subject of our first interview in the series.
Railveyor: Mike, thanks for sitting down and talking with us today. First, in your view, what are the benefits of Railveyor?
Michael Van Der Hooft: Every mine has a different kind of circumstance as far as haulage distance, amounts, mining method, particle size and so on. So between Railveyor, electric trucks and conveyor belts – they all have their own intrinsic places where they belong. The beauty for me always was that with Railveyor, it kind of fits in all of those little boxes.
There’s an optimum amount of tonnage. There’s a minimum and maximum. And I think it works very, very well when it comes to distance. It keeps your haulage costs down over long distances and medium kind of tonnage. It’s another tool in the toolbox. So is Railveyor good for every application? No. But it does have a lot of places where it does fit. And if it was utilized the way we did in the 114 experiment, you can see the benefits instantly.
RV: Speaking of the 114 experiment, can you tell us a little bit about your professional background and how you came to hear of Railveyor?
MVDH: I’ve been in the industry now for 48 years. I started on the tools. That’s where I grew up. I don’t have an engineering degree, but I’ve always been one of those people that looks for how can we do things better, how can we make things safer? How can we do the work more efficiently?
In my career I had I worked in lots of different places, done lots of different jobs. The people that were in charge of designing [Vale Copper Cliff] 114 and the president of the company wanted to pull a bunch of people together to work through basic designs that we would need as we developed this mine with Railveyor. At that time, we called the 114 project the “Mine of the Future.” So I was chosen to lead that group because of my mining experience and the fact that I knew a lot of people.
RV: What was the process of designing and planning the Copper Cliff 114 project like?
MVDH: We did a workshop. I think it was around 10 or 15 people that we had there, all miners, mechanical guys, technical people. And we just sat in a room and everybody took on a different aspect of Railveyor. And we said, “Okay, well, if we’re going to do this, we should do this. This is the method we would use to expand the system as we developed. These are the spacing of the cross cuts.” And so on. We talked about everything: infrastructure, labor, equipment, opening size, what kind of ground support we would put in.
We had a mandate to get 400 feet of development a week – we’d never seen that! But we said, “Yeah, that’s a great way to start!” And so I facilitated it with all the different groups, and I’d ask them questions: “How are you making out? Have you thought about this?” And so that’s where I started.
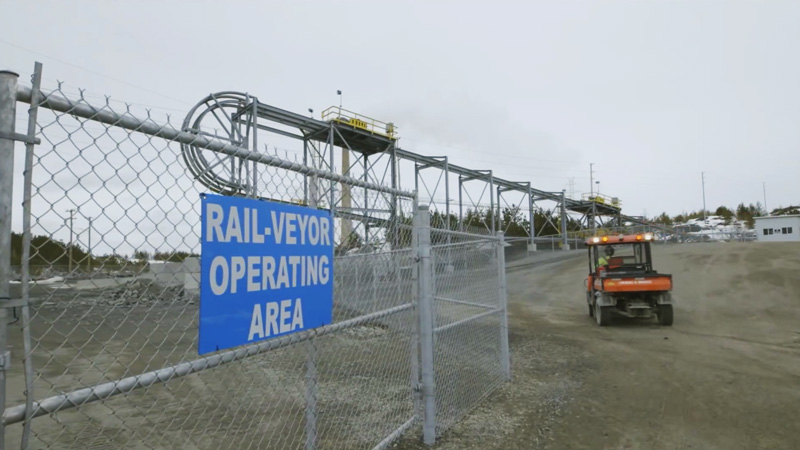
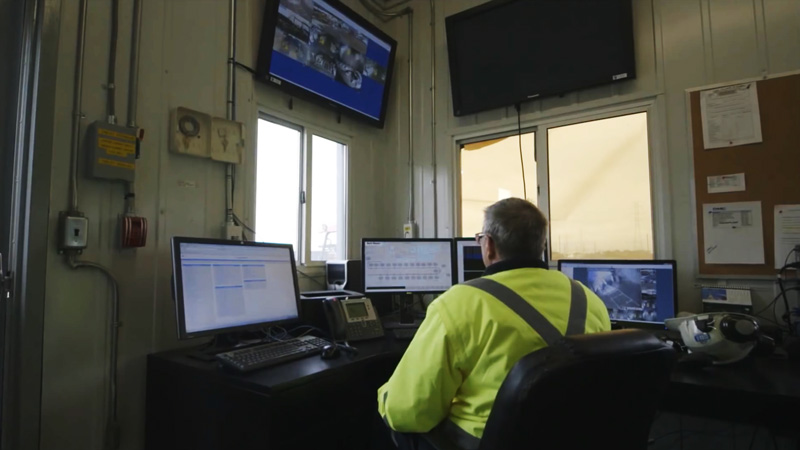
RV: When it was time to build the mine and run the experiment, what happened?
MVDH: So it had been about a year or a year and a half since the workshop completed and I’d been asked to go develop another department, which was all mine construction with our people. And they invited me back to lead the 114 project. At that time, I would have been the only person in Canada – well, myself and my cohort then, Dan MacIntyre – we would have been the only guys that worked on the design, the building and the operation of a Railveyor mine. So we had kind of a unique skill set at that point.
So we had a contractor, we had the OEM (which was Railveyor) and we had a Vale component. And when we came up against something that we saw as an issue or a problem, we would stop and say, “Okay, so how do we resolve this?” We brainstormed the solution, and we put it in action.
We had the opportunity to learn. We learned a lot about things like what’s important to measure. We started measuring percentage of face utilization. When we were making 400 feet a week, we were only utilizing the face 65% of the time… and therein lies an opportunity.
So we designed for 400 feet a week, but we realized very quickly that we could see much more if we worked through the issues with things like “how do we advance the electrical? How do we advance the the hardware within a Railveyor? What’s the timing of that look like? How do we maintain development of the ramps and construction of the Railveyor extension?” So those were all things that we learned as we went through this project.
We achieved the 400 feet a week. We actually got one week where we got over 500 feet a week – and we had 12 hour period where we had no power in the mine!
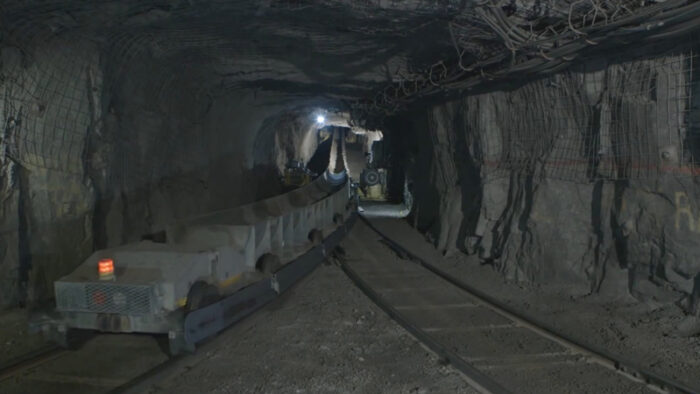
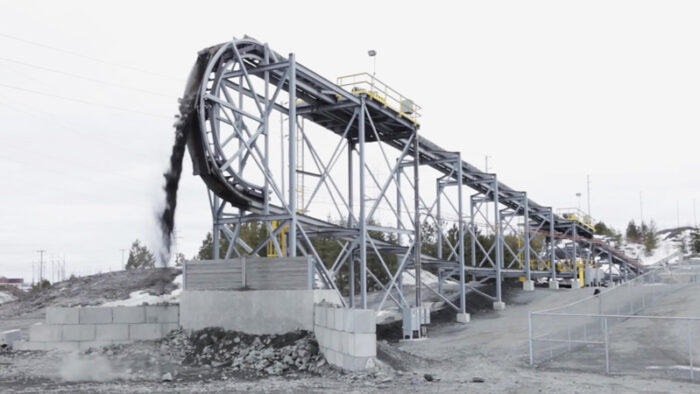
RV: That’s a great success. So as someone who led a very successful pilot program involving Railveyor, how would you design a mine from scratch today that would be an ideal use case for Railveyor?
MVDH: Ideal would be a ramp access mine – eliminate the shaft. The benefit is that by running a Railveyor, you run twin ramps, so you have a ventilation loop automatically. You’ve already established an escape way. Once you get to the ore body, you’re already ready to produce because you have an escape way in place. Legislation dictates you need escape way when you get there.
You can eliminate infrastructure needs like ore passes. Because you have a twin ramp, all the haulage traffic is in an independent ramp. So the other ramp ends being far more open for all of the other things you need to do in an underground mine: Move people, move material, etc. So that traffic becomes less congested and all your materials handling is in one ramp.
There’s no limit to the length, as we found. You can just keep going and going. You design of course for the ultimate length, but you don’t have to build it to that parameter yet. You can build [Railveyor] as you build the mine. It’s just got a lot of flexibility built right in it. It’s an autonomous operating muck handling machine!
RV: In your experience, how does Railveyor make an impact on safety in an underground mine?
MVDH: When we started in the Railveyor project, I guess I instantly saw the opportunities to do things better and to eliminate risk. There was lots of risk in a normal way of mining. I’ll give you one example: Ore passes. When you put your mindset into the idea that you’re not going to have any of those… that risk is gone.
It’s actually in the hierarchy of controls: Elimination is the best way to reduce risk, right? So when we were developing the mine, we always thought about those things that we could – by eliminating – make things that much safer.
The transportation system for material is completely independent from where men travel. So while now the industry is working on systems where the equipment will identify there’s a person in the area – well in this design, we eliminated the people away from the equipment. We got them away from the materials transport. So no big heavy trucks driving around with no visibility. It’s Railveyor. It drives autonomously in its own area.
When you’re a manager in an operation, you are always thinking about those risks. That goes with the territory. Because I know one thing for sure: Never, ever, ever do we want anybody to get hurt. Never. We don’t ever plan for that. We plan to make people safe. So in this design, it really was fulfilling that whole concept of a safe, clean, efficient operation. As a miner, that’s what I’d like to see the next generation move forward with.
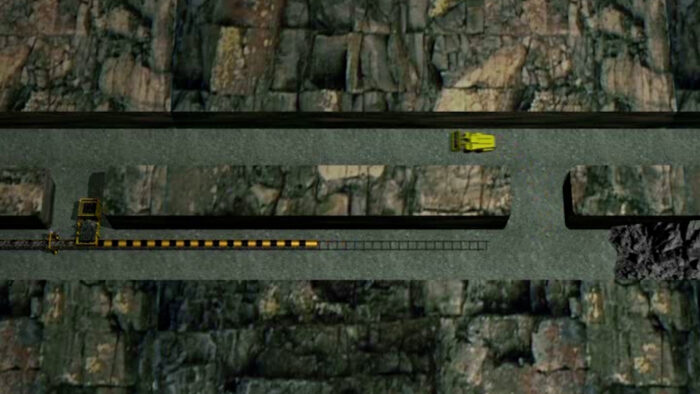
RV: Among competing options for materials transport in an underground mine, how do you think Railveyor stacks up?
MVDH: So there are pieces of equipment, trucks, for instance… they can be autonomous, but they require large openings. Our mines are going deeper, we’re mining lower grades. So the opening size needs to come down so you have less to worry about geotechnical stuff.
When I operated it, we used it for high speed development. So we were achieving rates that we would never achieve otherwise. Getting to the ore is the golden goose. You’ve got to get to the ore. That’s where the money is. That’s where the revenue is. If you can develop there quicker, that’s perfect. Once you’re there, you’re ready to produce. Like I said, you already have an escape way and you already have a material handling system. Just go. Move forward.
RV: Speaking of moving forward, as someone who has seen nearly five decades in the mining industry, how do you think Railveyor will be accepted by the next generation?
MVDH: Let’s be honest, the world is changing. The industry is very much ready for safe, clean mining. Reducing our carbon footprint is a big catchphrase. The generation that is coming is very attuned to that. My generation didn’t actually help that in a lot of ways. We weren’t on board. We didn’t understand it.
When we talk about design and operations and engineering and technology – this generation, they get it. They really do. My grandson is seven years old. I’ve had the iPhone for however many years they’ve been out. He does things with an iPhone I still can’t do!
So I think the generation that’s here now will take us to where we need to be. They will adopt the technologies. They have a much more open mind because they’ve lived through technology their whole lives. For me, when I started life, what was a cell phone? Never heard of it.
Now there’s more computing power in my cell phone than there was in my first computer. So, you know, I think this generation will absolutely get it. They will take the technology to the levels it needs to be for mining, for anything in this world. They will make it happen, definitely. And they’re open to it.
We’d like to thank Michael Van Der Hooft for allowing us to interview him and for telling such an interesting story about developing the Railveyor pilot program at Copper Cliff 114. Of course, our technology has come a long way since those pioneering days. We’ve taken the lessons learned by Michael and a host of other collaborators and customers to fully commercialize the Railveyor system and deploy it in locations around the globe.
If you’re interested in how Railveyor can revolutionize new mine design at your company or fit into an existing application for the best in safe, clean and profitable material handling, please contact our team today by filling out the form below.